Proposed solution
The predictive control algorithms proposed to be developed will be amended to include two components of the objective function, one economic and one for control. By rewriting the objective function so as to include a measure of energy consumed could exploit the fluctuation in the conditions of operation with significant savings of energy at the same time maintaining a margin of safety in operation. Control algorithms will be implemented in both the classical variant in which the design parameters are calculated on the basis of apriori knowledge of the process model and in the adaptive control variant in which the command generated by predictive algorithms is based on an updated model on the process measurements, at each sampling period.
In addition to the implementation of advanced algorithms of automatic control for the biological treatment plant this project proposes a hierarchical control for the entire system. Hierarchical control systems do not exclude conventional systems but they include and
extend them by offering them decision-making capabilities.
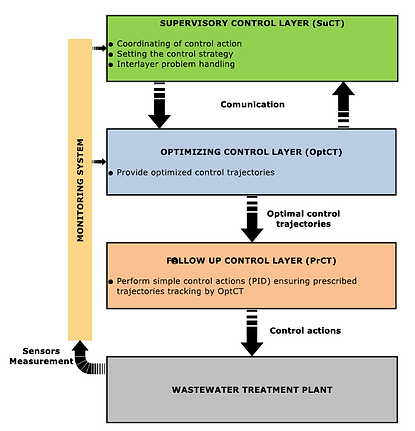
The main elements of the hierarchical structure are: the monitoring system, the supervisor layer (SuCT), the optimization layer (OptCT) and the process control layer (PrCT) that contains PID controllers. The OptCT implements an optimization technique for predictive control and MPC will generate references for the lower control loops in order to optimize the performance. The objectives of the OptCT control can be divided into long-term, medium term and short term objectives. Different time horizons of the objectives are determined by the different time scales of the dynamics of the biological wastewater treatment plant and by the variability of the input disturbances. There are various ways to control each time scale. These depend on the chosen control strategy and will, therefore, depend on the objective function and on constraints associated with it. In order to be able to generate effective action, OptCT must have the following information: the current state of the system and a prediction of the disturbances together with information regarding the constraints. The first two are provided by the monitoring system. In general, the monitoring does three major activities: collecting of measurements, estimation and prediction. When we refer to the resolution, it depends on the dynamics of the variables being monitored, time scales and measuring equipment. SuCT is responsible for coordinating the operation of all levels by selecting the functions and constraints for the MPC and OptCT. The supervisor will assess the situation of the plant permanently, will update the model and the control parameters, will make decisions in order to reach global objectives
for control loops, will ensure that the values are within the normal levels and will provide the management of alarm situations. Information from all other units in the control structure are available to SuCT at any time. Therefore, SuCT has global knowledge of the current activity of the entire system. It will ensure that the control actions are the most effective and will give appropriate response to the occurrence of unwanted events in the system. On the base of the information provided by the monitoring system, the level of optimization and the level of control, the supervisor will generate a control strategy to be applied at the current time.
The level of process control is responsible for following the references computed by the optimization layer. For the adjustments of the conventional loops (simple loops for level, flow, dissolved oxygen, etc.) we will use PID controllers (PLC incorporated), whereas for complex (large time constants, dead time, variable parameters, or pronounced nonlinearities) or multivariable loops we will use predictive controllers. Another novelty item of this project proposal is the implementation of predictive control algorithms on the programmable logic controllers (PLC). The proposed solutions will be implemented and tested in the current operating conditions on the waste water treatment plant in operation at P3 partner. The technology and the functionality of the plant will be analysed; measurements will be made and the plant working parameters will be evaluated. We will analyse the possibilities for adaptation and implementation of advanced control algorithms, develop the control system according to the possibilities of intervention in the process, choose the structure with the best chances of success and implement this control system. Afterwards, the efficiency in operation will be tested and analysed.
Figure 1. General view of hierarchical control structure
Original and innovative contribution of the project
Starting from the weakness of wastewater treatment plants used now, where the biological processes usually take place in a conservative manner, the implemented control systems dealing just to maintain the quality parameters of de discharged water from the wastewater treatment plant between some setpoints, this project proposal comes with a new approach for the problem: ensuring the operability of the wastewater treatment plant and reducing the pollution when discharging into emissary taking into account physical and economic constraints.
The adopted solutions are original and they cannot be seen in any other wastewater treatment plant from Romania. The solution that we propose is based on existing equipment, the need to add others will depend on the needs of the plant, and the control algorithms that are going to be implemented are software solutions applicable in the pilot plant, but having a high adaptability degree for other applications (other constructive types of treatment plants). The solutions proposed to solve the current problems are innovative due to the software and hardware solutions adopted and the requirements of the technological process of the owner, where the control system is implemented. They are in respect with the objectives and the priorities of the National Plan for Research – Development and Innovation 2007-2013 PNII
Original elements:
-
Development of a modelling and control platform, that solves some of the existing problems through a unified approach to modelling and control of wastewater treatment processes. As original elements here we highlight: the development of modelling techniques for control for the subsystems that make up the wastewater treatment stations; development of modules for advanced control based on models apriori developed; definition of statistical indicators for the evaluation of control performances; integrating them together into an global model that can evaluate the control algorithms developed during the project.
-
Introducing the concept of aided design of the control system. The simulation platform allows determining the optimum operating strategies, making some efficient and safe control strategies and calculating the design parameters for automatic control systems in a short time.
-
Analysis of technology and functional particularities of the treatment plant, calibration and validation of the model based on data obtained from process measurements
-
analysis of the influence of the concentration of the dissolved oxygen on the water quality at the outlet of the treatment station, the quality of the slurry, the biological activity of micro-organisms as well as the energy consumption of the control strategy for determining the concentration of dissolved oxygen.
-
Development and implementation of multivariable predictive control algorithms combined with feed-forward compensation of the measurable disturbances and rewriting of the objective function of the predictive algorithms by including energy consumption
-
Development and implementation of adaptive control techniques, especially for nonlinear predictive control using neural networks for process modelling
The final version of the control system will integrate hardware and software applications that will solve the current problems. The final configuration is based on advanced design techniques for control and supervision, on digital electronics, on the realization of specialized control structures and the use of programming tool for ensuring real-time operation.
The savings made by using this control system and automatic control of wastewater treatment plants can be calculated and will be presented directly in the research project. Such a control system for wastewater treatment plants does not exist in Romania, so by default it will be a reference for many applications in the field of environmental technologies.
To meet the up mentioned objectives of the project it is considered as the advanced control strategie the model based predictive control (MPBC).
Objectives
In this project, a series of improvements in controlling the operation of the wastewater treatment plants are proposed in order to meet the requirements of increased efficiency. The goal of this project is the development and implementation of control strategies based on advanced techniques of automatic control to enable the following three main objectives:
-
optimizing the quality parameters of de discharged water from the wastewater treatment plant,
-
reduction of costs;
-
ensure biological reliability and maintain the quality of the water discharged into the effluent in operating conditions.